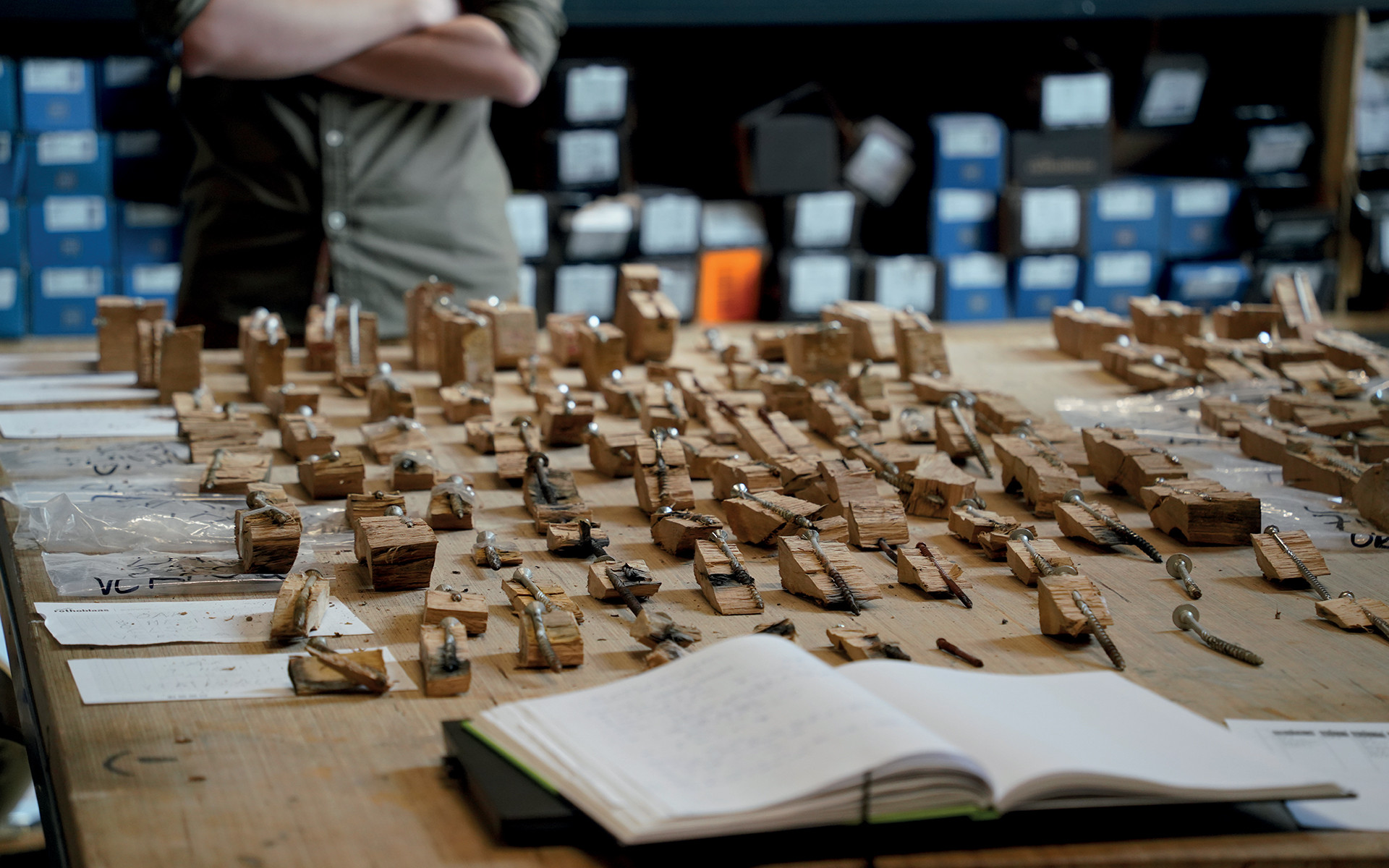
Timber screws: a guide to risk factors
When designing or building a timber structure, the choice of screws can determine whether an element lasts for decades or succumbs to rapid deterioration. Humidity, the presence of chlorides, atmospheric pollution and even the chemical composition of the timber itself are all variables that determine the screws’ exposure to corrosion. If ignored, these variables can compromise the overall stability of a structure and significantly increase maintenance costs.
Timber screws come into direct contact with environmental and chemical factors that, when particularly aggressive, can initiate corrosion processes visible within just a few weeks. It is therefore essential to understand service classes (which describe the temperature and humidity conditions) and corrosivity classes (both atmospheric and timber-related) to identify the most suitable materials and coatings.
Below, we provide an overview of the main risk factors, as well as guidance on the most common wood species and types of steel, to help you make informed decisions when selecting timber screws.
Corrosion in timber screws: what it is and when it happens
Corrosion is the deterioration of metal, which occurs when screws come into contact with moisture and chemicals in the environment or timber. The main factors accelerating corrosion are:
Relative humidity: the more humid the environment, the faster the corrosion process.
Chlorides: common in coastal areas or regions where de-icing salts are used, they promote localised corrosion processes.
Airborne pollutants: substances such as sulphur dioxide and nitrogen oxides found in highly urbanised settings, such as megacities or near industrial plants, can significantly accelerate corrosion.
Chemical characteristics of the timber: acidic pH or chemical and thermal treatments (such as copper-based treatments or flame retardants) substantially impact screw oxidation.
Focusing only on the exposed portion of the metal while ignoring what’s happening inside the timber, or vice versa, can lead to incomplete and potentially hazardous assessments. That's why it’s essential to understand the environment and substrate in which the screws will be installed before selecting the timber screws.
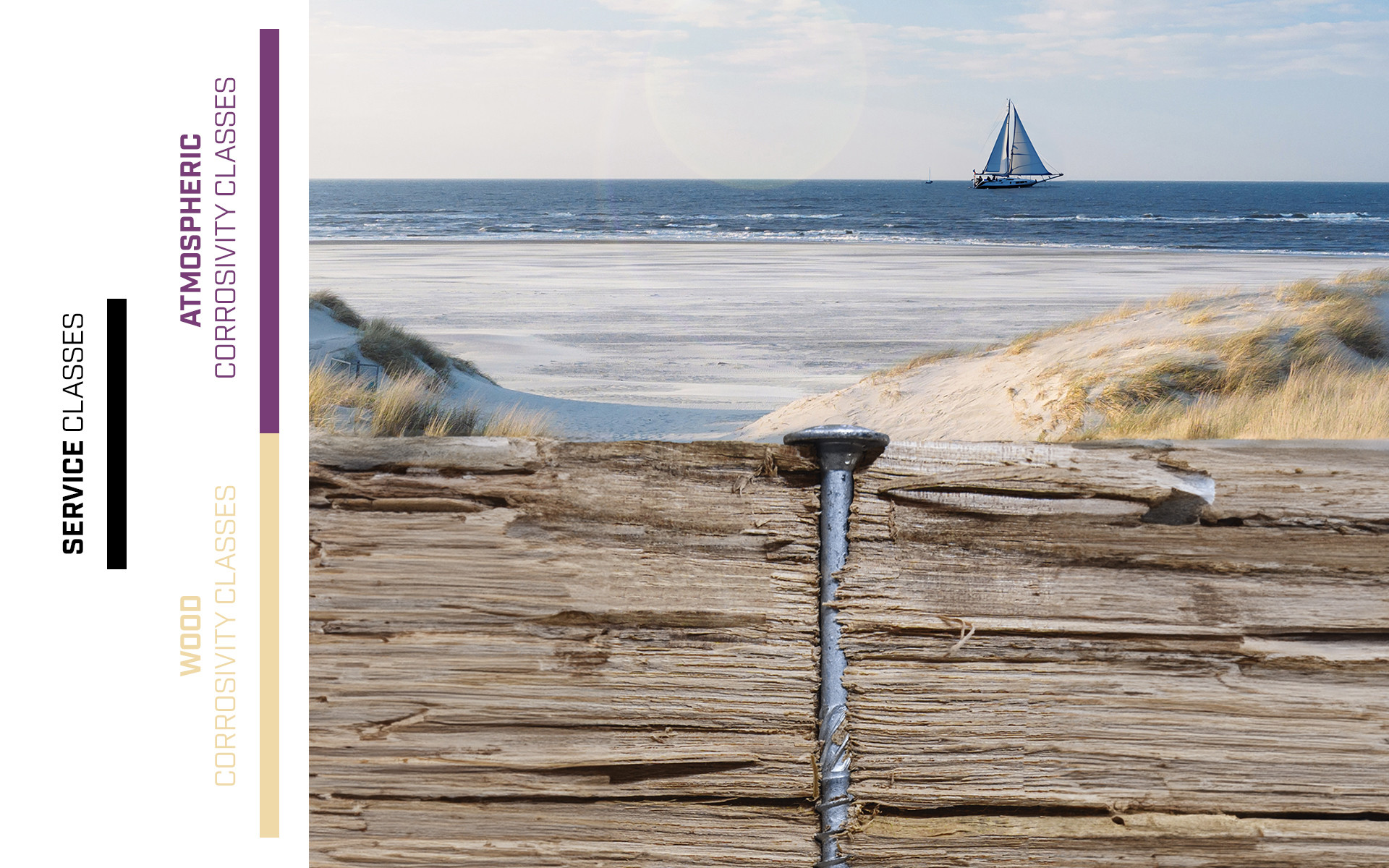
Service classes and corrosivity classes: atmospheric and timber-related
The reference standard (EN 14592:2022) classifies exposure conditions into service classes and corrosivity classes, helping engineers and builders make informed choices.
Service class
The service classes (SC1, SC2, SC3, SC4) describe the timber’s moisture content based on the temperature and humidity conditions of the environment:
SC1: elements in indoor environments with low and relatively stable humidity levels. Moisture fluctuations are minimal.
SC2: elements in partially covered areas or exposed to moderate humidity. This includes porches or semi-protected structures, where timber can occasionally absorb moisture.
SC3: elements exposed to the outdoors or high-humidity contexts. Temperature and humidity fluctuations are significant, and the moisture content in the timber reaches high levels.
The U.S. (NDS) and Canadian (CSA:O86) standards define similar exposure conditions to those in the service classes:
DRY conditions: equivalent to SC1 and SC2, with humidity levels up to 19%.
WET conditions: equivalent to SC3 and SC4, with humidity levels exceeding 19%.
Knowing the service class helps assess how much water the timber absorbs over time. The higher the moisture content, the greater the risk of corrosion for timber screws.
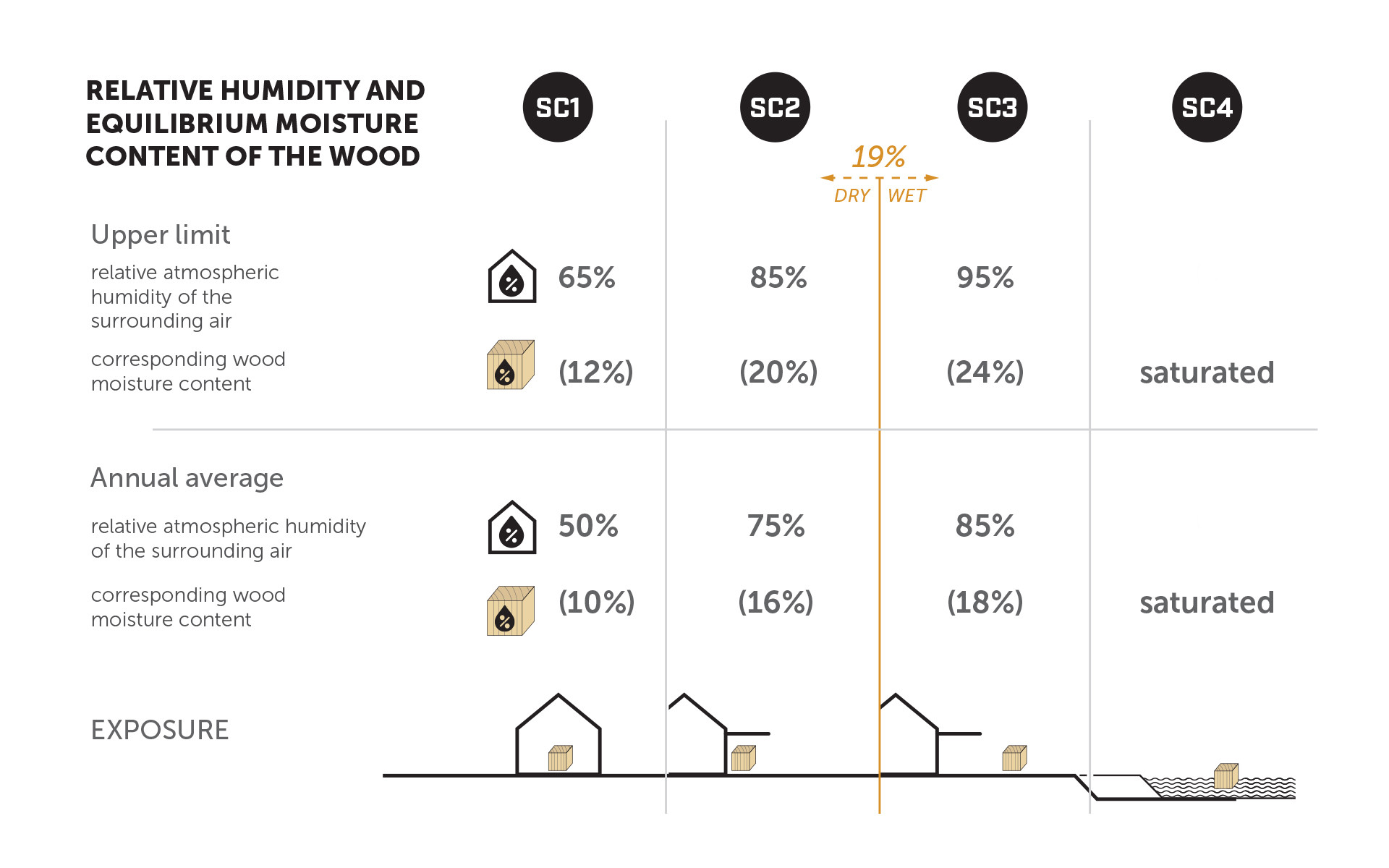
Atmospheric corrosivity classes
The EN ISO 9223 standard classifies atmospheric corrosivity into five categories, ranging from C1 (very low) to C5 (very high). These categories take the following into account:
Pollution: the presence of harmful agents in the air (such as sulphur dioxide or chlorides).
Humidity: the frequency and duration of exposure to rain, fog or condensation.
For example, a C5 environment is typical of coastal areas or industrial zones, where salt spray and chemical fumes accelerate the corrosion of timber screws. In a C1 environment, such as a well-protected indoor space, the risk of corrosion is minimal and screws with lighter coatings can be used.
Timber corrosivity classes
The EN 14592:2022 standard similarly classifies the corrosivity of timber into five categories, ranging from T1 (very low) to T5 (very high).
The timber corrosivity class depends on:
Acidity and wood species: different wood species contain varying levels of acetic acid, which acts as a corrosive agent on metals within the timber. The quantity of this acid determines the pH of the wood species. The lower the pH, the more aggressive the wood species.
Thermal and chemical treatments: impregnating treatments, flame retardants, copper salts or chlorides alter the reactivity of the timber when in contact with metal.
Moisture within the timber: a high moisture content promotes the spread of corrosive substances all the way to the screw’s surface and increases the electromechanical reaction that occurs during corrosion.
Essentially, a comprehensive assessment of service class, atmospheric corrosivity class and timber corrosivity class provides a clear picture of the conditions that timber screws will be exposed to.
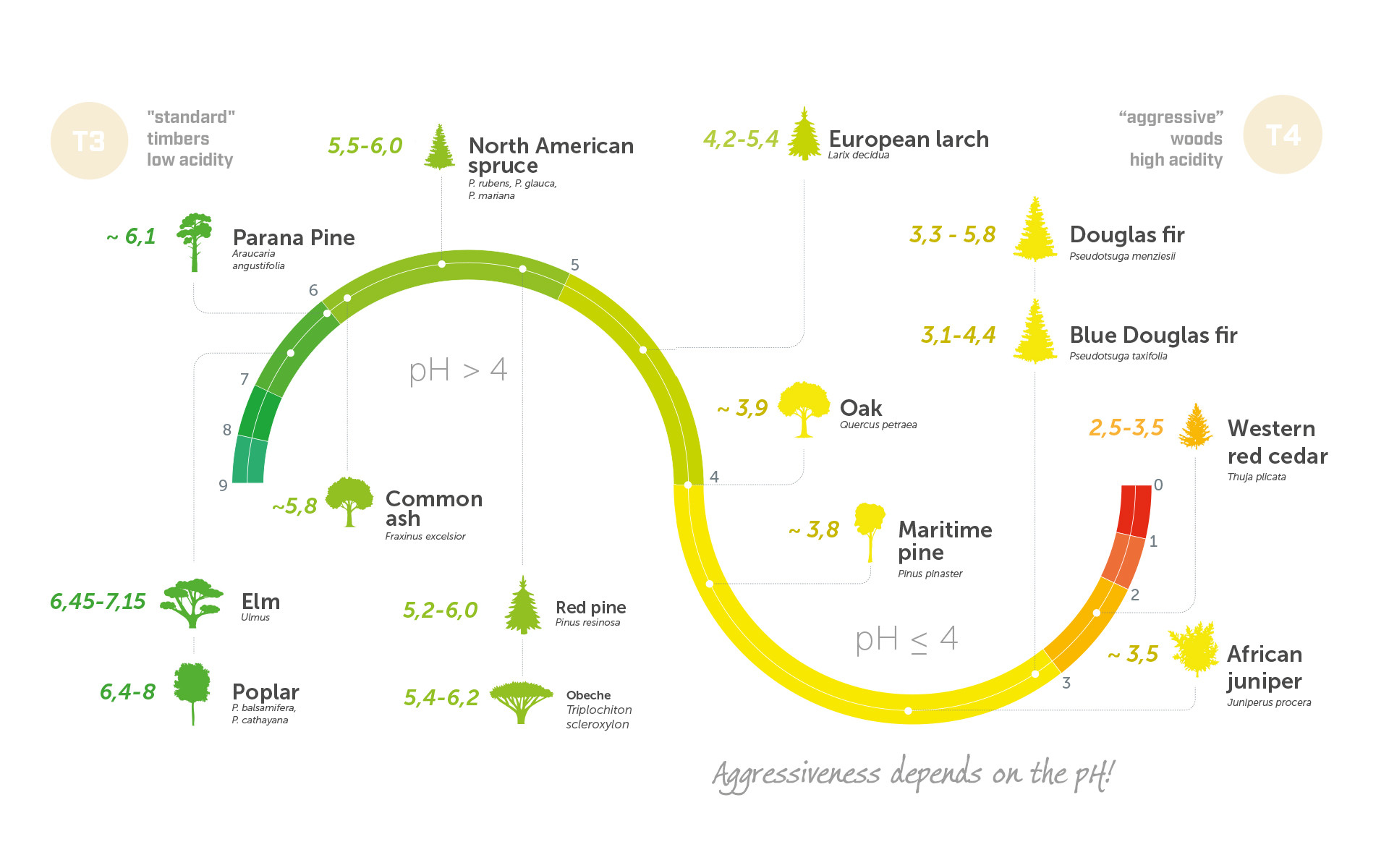
Wood species: tannins and pH to consider when selecting timber screws
Not all types of wood react in the same way when in contact with metal. Some species, such as oak, have high levels of tannins, substances that can form a protective film on the screw. However, in wood species with a particularly acidic pH (below 4), or in humid environments, even oak can promote corrosive reactions. Here are two examples:
Oak:
Very high tannin content, which can locally reduce the rate of corrosion.
In high humidity conditions (SC3 or WET), its acidity accelerates corrosion.
Fir:
Low tannin content.
Less aggressive in terms of pH, making it much less corrosive in humid environments.
Although tannins are often associated with corrosion – since many tannic woods are also acidic (pH < 4) – the most important factor in the corrosion process within the timber is the corrosivity class (T), which depends on pH and moisture content.
Evaluating the wood species, its pH, and any treatments (such as chlorides or copper salts) is therefore a key step in choosing the right timber screws. In highly acidic environments, stainless steels with high corrosion resistance (such as AISI 316) can be the most reliable solution.
What happens to timber screws in different corrosive environments: experimental study
An effective way of understanding how the environment affects corrosion is to conduct full-scale tests. In the R&D lab, an experimental study was performed on approximately 350 timber screw configurations, exposed for one year to different conditions.
Experiment set-up
Materials tested: 6 types of screws, ranging from bright zinc-plated carbon steel to various grades of stainless steel.
Conditions:
Wood species: oak
Service class: SC3
Atmospheric corrosivity class: C2 (low, but not negligible aggressiveness).
Timber corrosivity class: T4 (high tendency for corrosion due to wood acidity).
Results
After 1 month:
The zinc-plated screws started developing tannin marks on the surface, particularly along the thread.
The stainless-steel screws (AISI 410) showed no signs of oxidation.
After 10 months:
The zinc-plated screws showed clear signs of red surface rust.
The stainless-steel screws (AISI 410) had tannin marks but no rust.
This test demonstrates how crucial installation conditions and wood type are. Even a coating designed for a certain level of exposure may not be sufficient if the overall corrosivity (considering both atmospheric and timber-specific conditions) exceeds expectations.
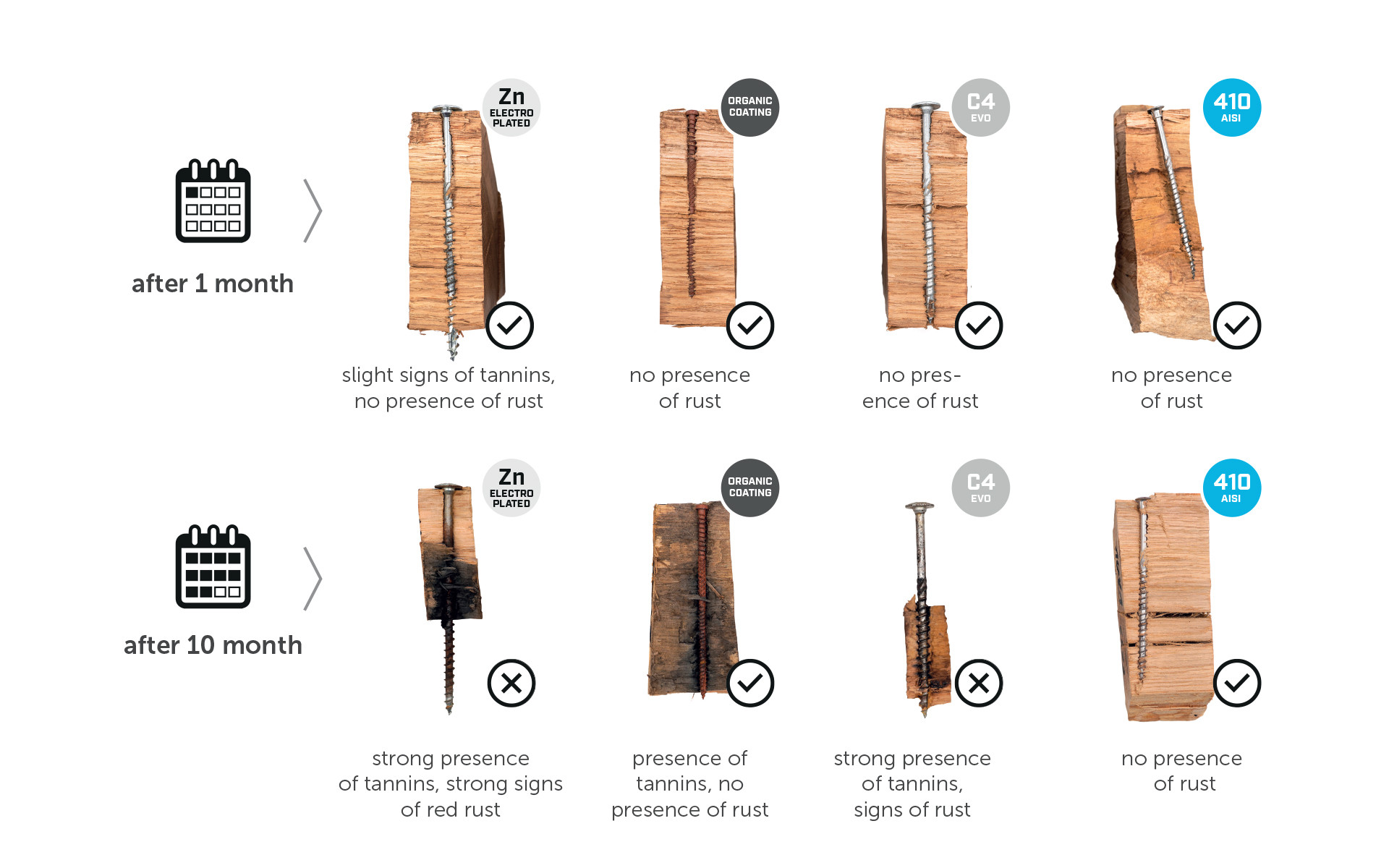
Steels and coatings for timber screws: how to choose the right ones
Anyone who works in construction knows that there is no such thing as a universal screw. Each context requires a specific material and coating. Generally speaking, timber screws fall into two main categories: carbon steel with coating (zinc plating or advanced treatments) and stainless steel.
Carbon steels with coating:
These are often the most cost-effective solution, offering high mechanical performance.
They offer variable protection, however, depending on the type of coating. This can range from basic electro-galvanisation to C4 EVO or C5 EVO coatings, designed for highly aggressive environments. The C4 EVO coating has been developed to provide high performance in harsh atmospheric conditions. In aggressive timber conditions, however, stainless steel is the only reliable option.
They require a detailed analysis of real conditions, as they may corrode in humid environments rich in harmful substances.
Stainless steels:
HCR: offers the highest corrosion resistance, even in the presence of chlorides and pollutants. It is the recommended choice for extreme environments, such as indoor swimming pools.
AISI 316 (A4): suitable for marine or industrial environments, where screws are exposed to salts, pollutants and highly aggressive timbers (T5).
AISI 304 (A2): a cost-effective alternative for demanding, but less extreme conditions than the above. High resistance to acidic timbers (T4).
AISI 410: a martensitic stainless steel with good mechanical properties and moderate corrosion resistance (provided it is kept away from chloride sources). It is ideal for a balance between strength and durability. Preliminary tests show good resistance in acidic timbers (T4).
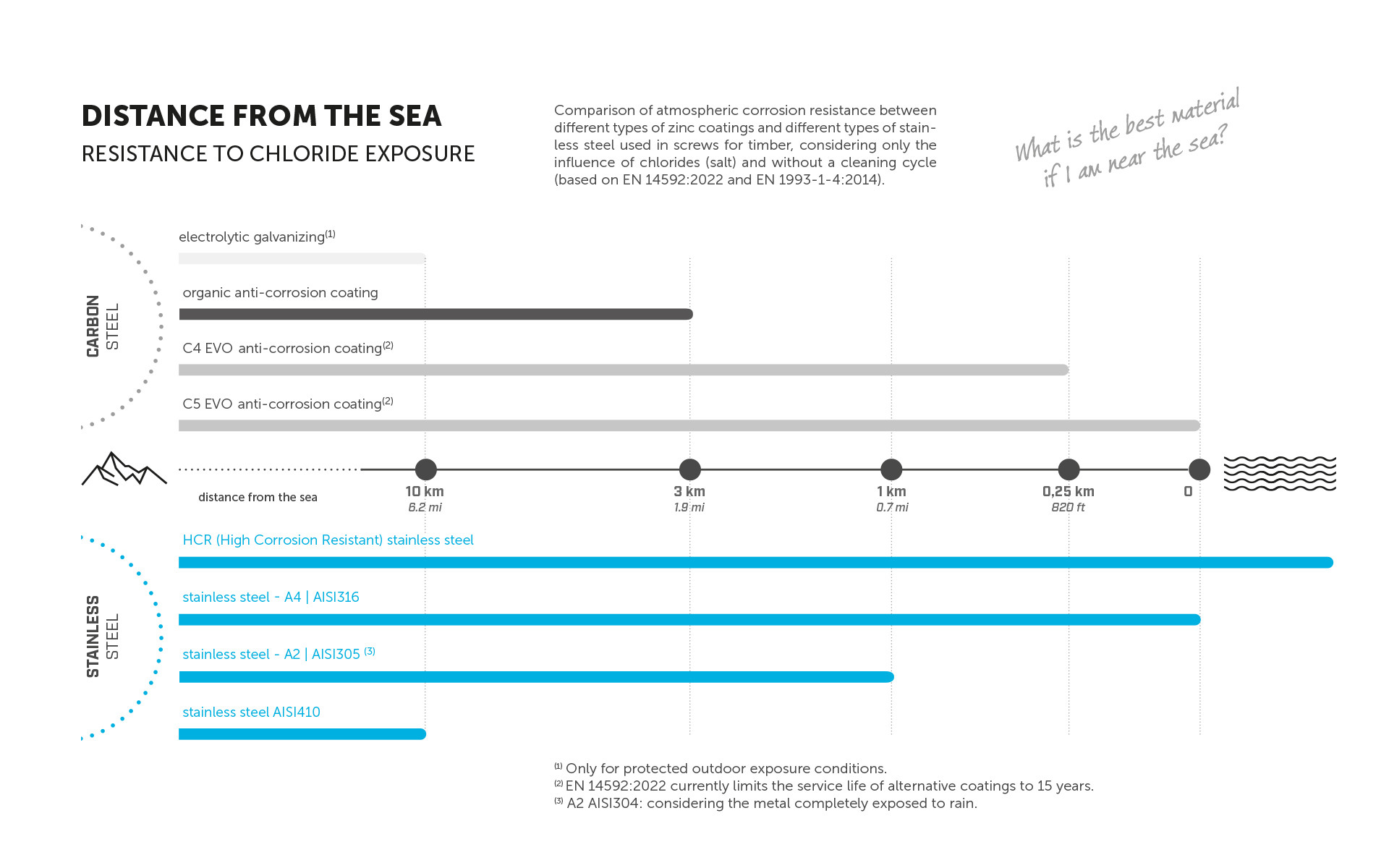
The Rothoblaas coating selection chart and dedicated video lesson: two essential tools
Given the many factors that influence corrosion, and all the variables that can trigger or accelerate corrosive processes, we have compiled a user-friendly reference chart showing how different materials and coatings perform based on their environmental and timber corrosivity classes (based on EN 14592:2022 and EN 1993-1-4:2014, available here and in the Smartbook Timber Screws.
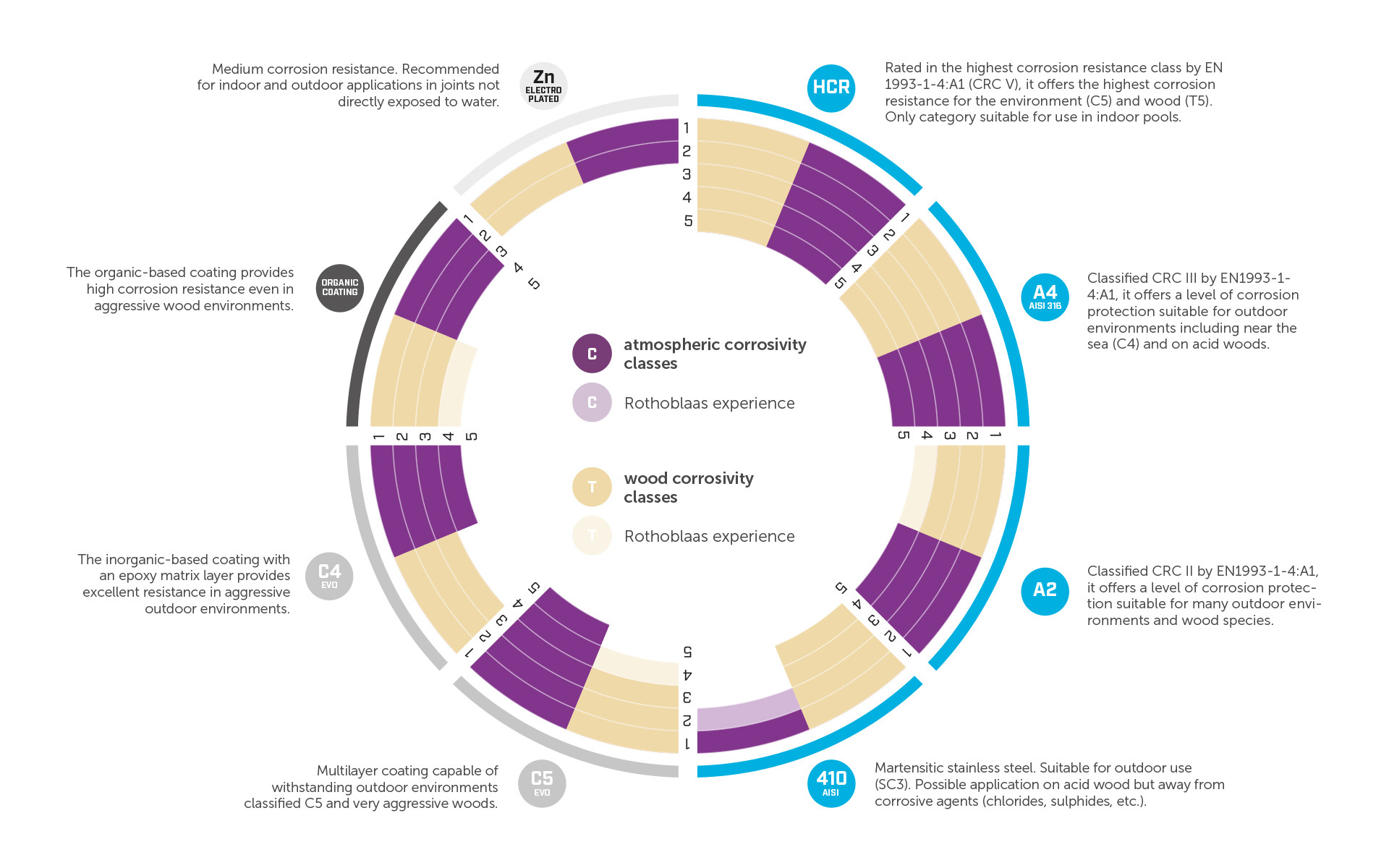
The complexity of this subject drives us to continuously test our products and invest in research and development to deliver increasingly high-performance solutions, while also equipping industry professionals with the essential tools to fully understand how and when to use Rothoblaas screws.
This is also why we have created a video lesson, which provides a more detailed explanation of some of the topics covered in this article, along with additional insights and data to help gain a deeper understanding of this subject.
All rights reserved
Technical Details
- Year:
- 2025
- Country:
- Any
- Products:
- HBS EVO VGS EVO HBS VGZ EVO SHS SHS AISI410 HBS HARDWOOD TBS EVO TBS VGZ VGS KKT A4 | AISI316 KKF AISI410 HBS PLATE A4 HBS PLATE EVO HBS PLATE KKA AISI410 HBS EVO C5 SCI HCR