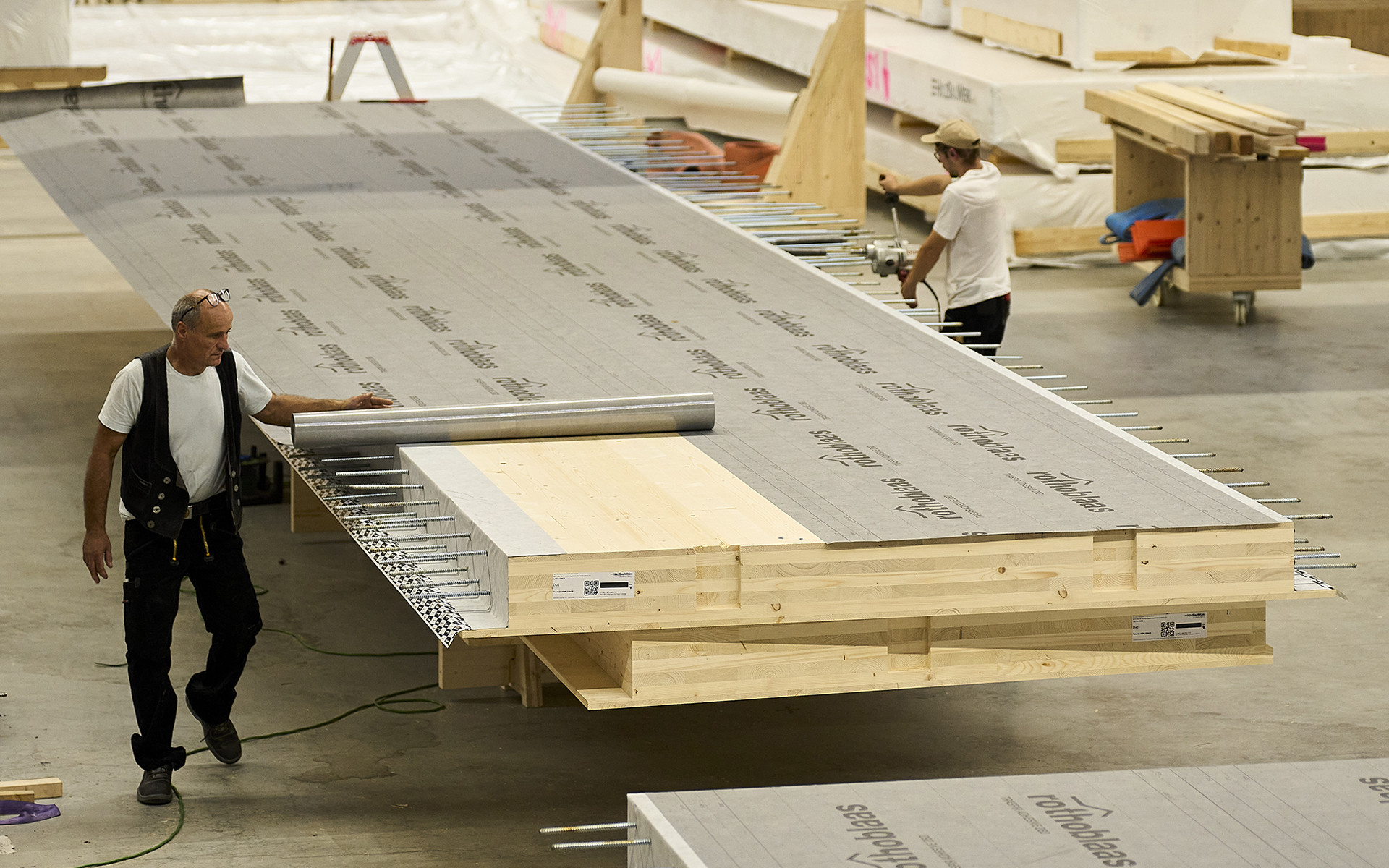
What is Design for Manufacture and Assembly
What is DfMA?
Design for Manufacture and Assembly, known as DfMA, is an engineering technique that aims to improve the efficiency of the building process from design through construction, while also reducing overall construction costs and times.
The method is based on two essential principles: the ease of manufacturing components and the efficiency of their assembly into the final configuration.
To achieve these objectives, these needs must be considered right from the initial planning stages.
In the past, DfMA was traditionally split into two distinct methods: Design for Manufacturing (DFM) and Design for Assembly (DFA).
DFM focused on selecting the most cost-effective construction processes, materials and techniques, as well as simplifying production processes as early as the design stage, when issues can be most effectively addressed with the least impact on costs.
DFA, on the other hand, aimed to reduce assembly times, costs and overall complexity by optimising the number of components and assembly steps, while also minimising variations in build quality.

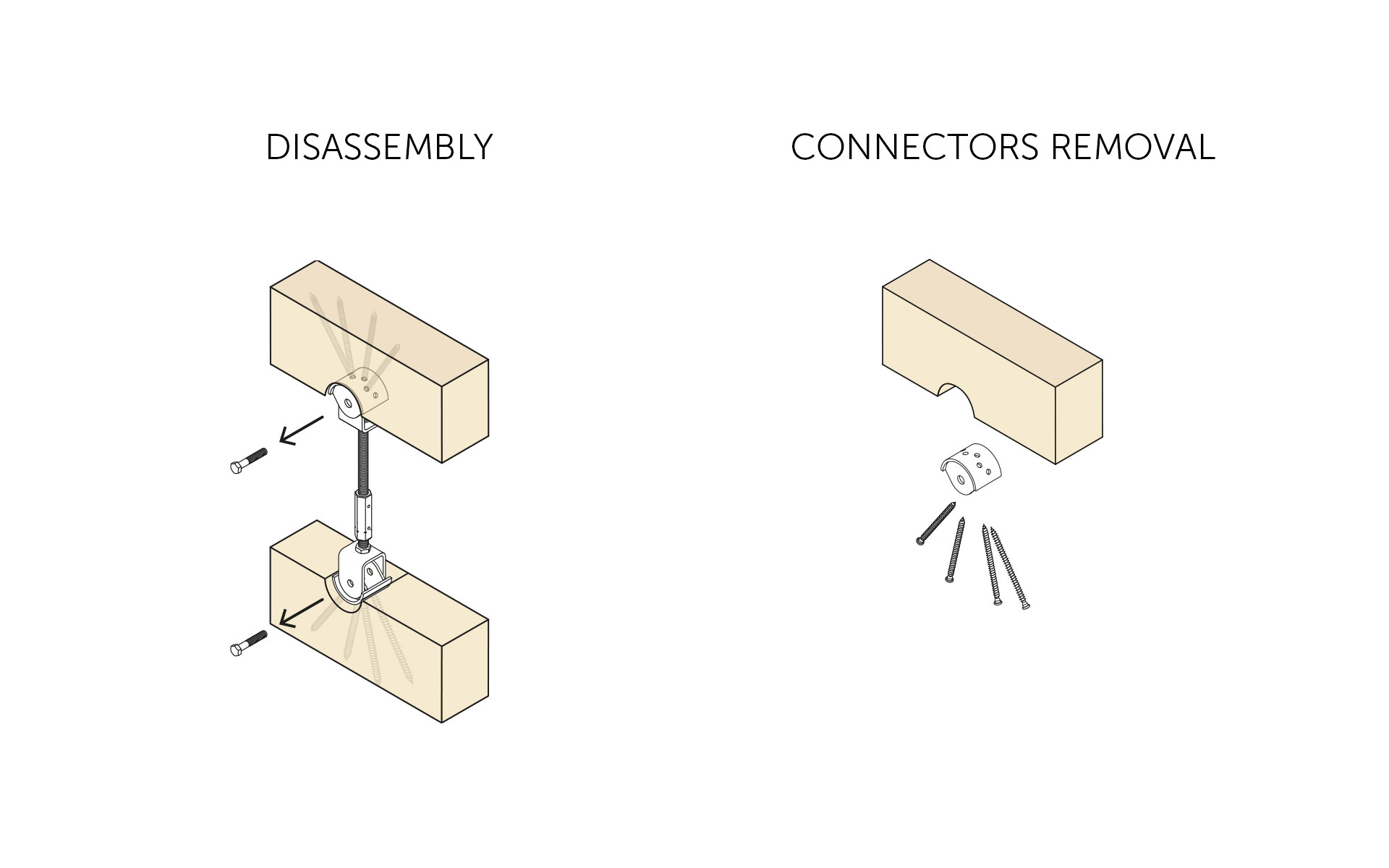
Which factors to consider for DfMA?
For DfMA to be effectively implemented, several key factors must be considered:
Planning Careful planning is the first step towards successfully transitioning to this construction method. Consulting with the production network, or at least its key components, during the design stage is crucial in identifying opportunities for cost reduction right from the “birth” of the building project.
Materials Choosing materials compatible with scalable and modular construction is another crucial element. The choice of raw materials will determine the production processes and means, as well as the timing and approach to quality control. With this in mind, shortening the supply chain as much as possible proves pivotal in ensuring efficiency.
Processes Being familiar with the construction process is essential in reducing costs. For example, prefabricating certain building components minimises the on-site handling of numerous separate elements in favour of fewer monolithic components, thereby reducing complexity and associated costs.
Standardisation Using standard parts or components can significantly reduce the cost of new projects, while also improving inventory management and time-to-market. The “D” in DfMA is vital: if the design falls short, the desired results will never be obtained.
Design for Manufacturing and Assembly and timber construction
Timber constructions, thanks to the possibility of completely dry assembly and the precision of CNC cutting, are particularly suitable for prefabrication and modularity.
Prefabrication means assembling part of the building components at a location other than their final destination, like at a production plant, before transporting them to their final place of installation, where they are assembled in a few simple steps.
Operating from the production plant improves both speed and efficiency with benefits in terms of costs, the quality of work and quality of life of tradespeople.
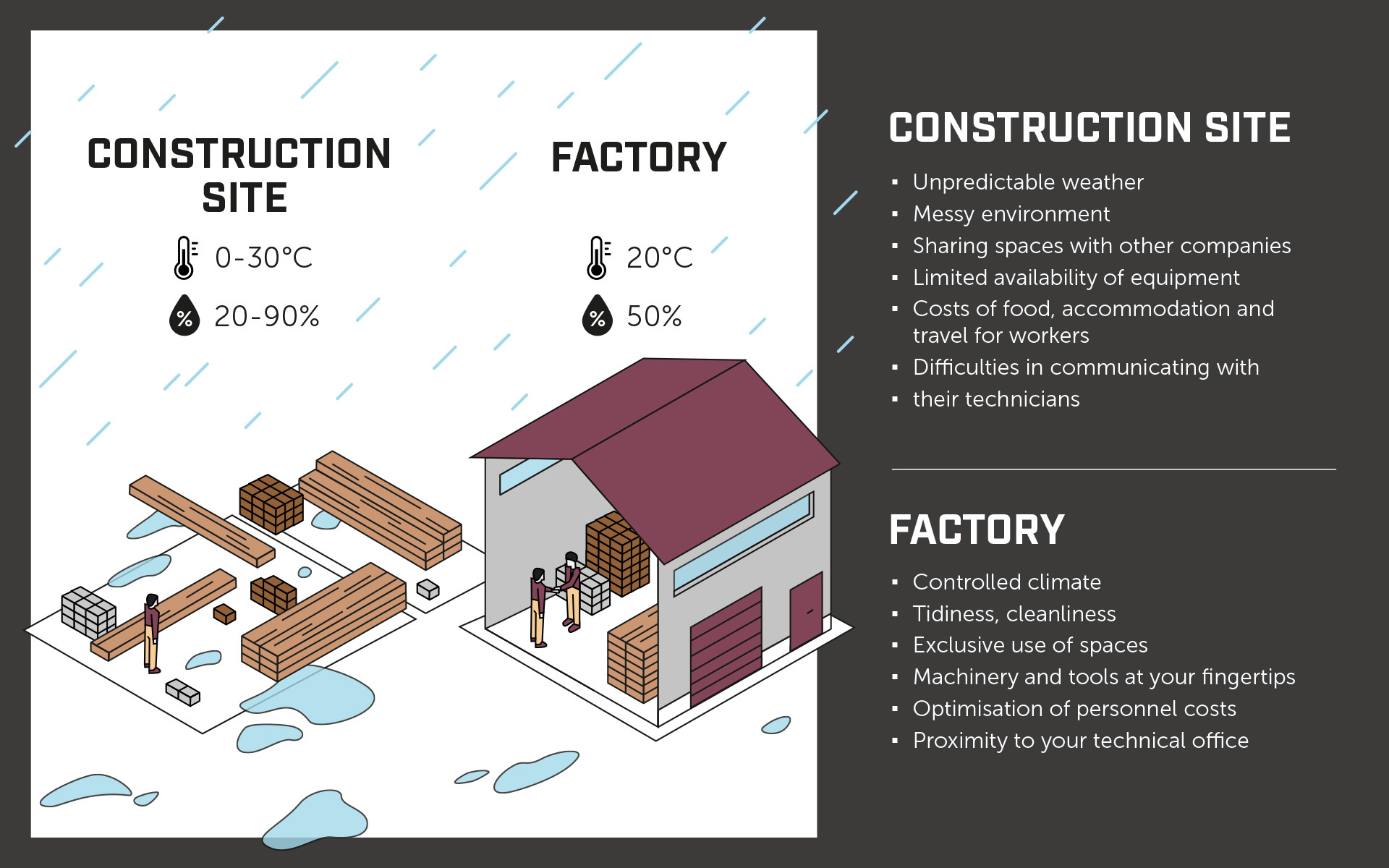
The Rothoblaas approach to DfMA
In this context, Rothoblaas develops both integrated solutions to protect the construction elements from the plant to the construction site through the completed building, as well as pre-engineered, standardised and scalable connections based on a small number of similar connectors.
These technologies allow the use of modular systems compatible with prefabrication, improving the efficiency of the construction process, minimising waste and reducing the risk of error.
DfMA also depends on the possibility to implement as many solutions as possible prior to assembly, as demonstrated by this Design for Manufacturing and Assembly case study completed by Holzbau Layh:
Types of prefabricated construction and timber construction products in Design for Manufacture and Assembly.
Prefabrication can be applied in different ways and with progressively more advanced levels: let's see some of them.
Pre-assembly of compound structural elements:
Structural elements consisting of multiple timber components can be pre-assembled at the plant. One example is ribbed timber floors (rib panels or box panels). Dry assembly with SHARP METAL allows the disassembled floors to be transported in containers and then the ribbed section to be rebuilt on site.
Pre-installation of connections on structural elements
Some connection systems allow pre-installation of the connector at the factory. The small footprint of the connectors ensures space is optimised during transport and reduces the risk of damage during handling. Connecting the elements on site then becomes fast and efficient, like in this case with LOCK FLOOR
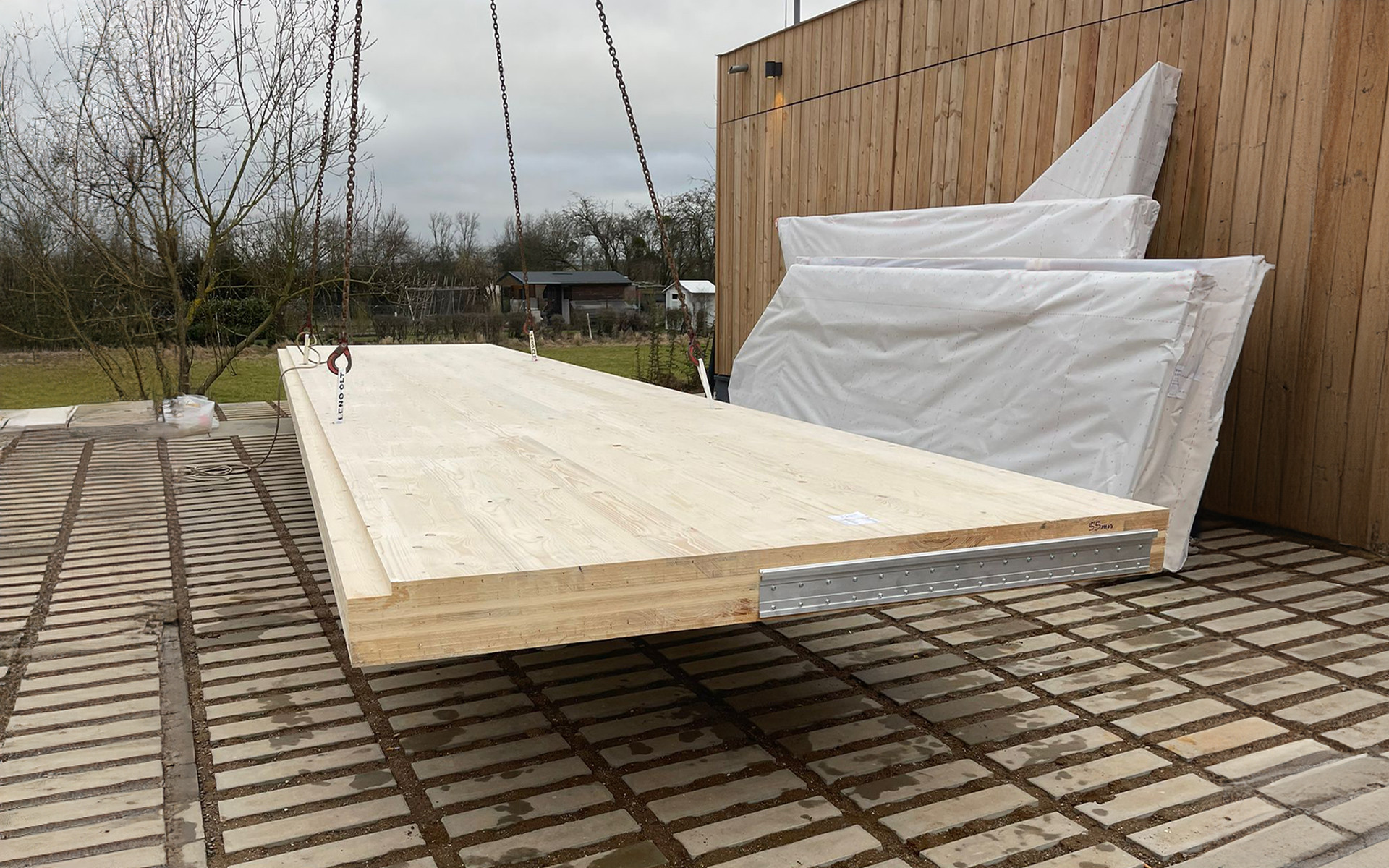
Prefabricated constructions with flat (or two-dimensional) modules
One particularly advanced technique for prefabricated buildings involves manufacturing flat components such as walls, floors or roofs at the plant. These can then be transported to the construction site and assembled with varying degrees of prefabrication:
• Structural 2D modules, comprising only the load-bearing structure, with the possible addition of insulating materials or waterproofing.
• Complete 2D modules, which partially or fully include the finishes and possibly even systems engineering components. Rothoblaas offers numerous connection systems tailored for these applications, such as the new RADIAL.
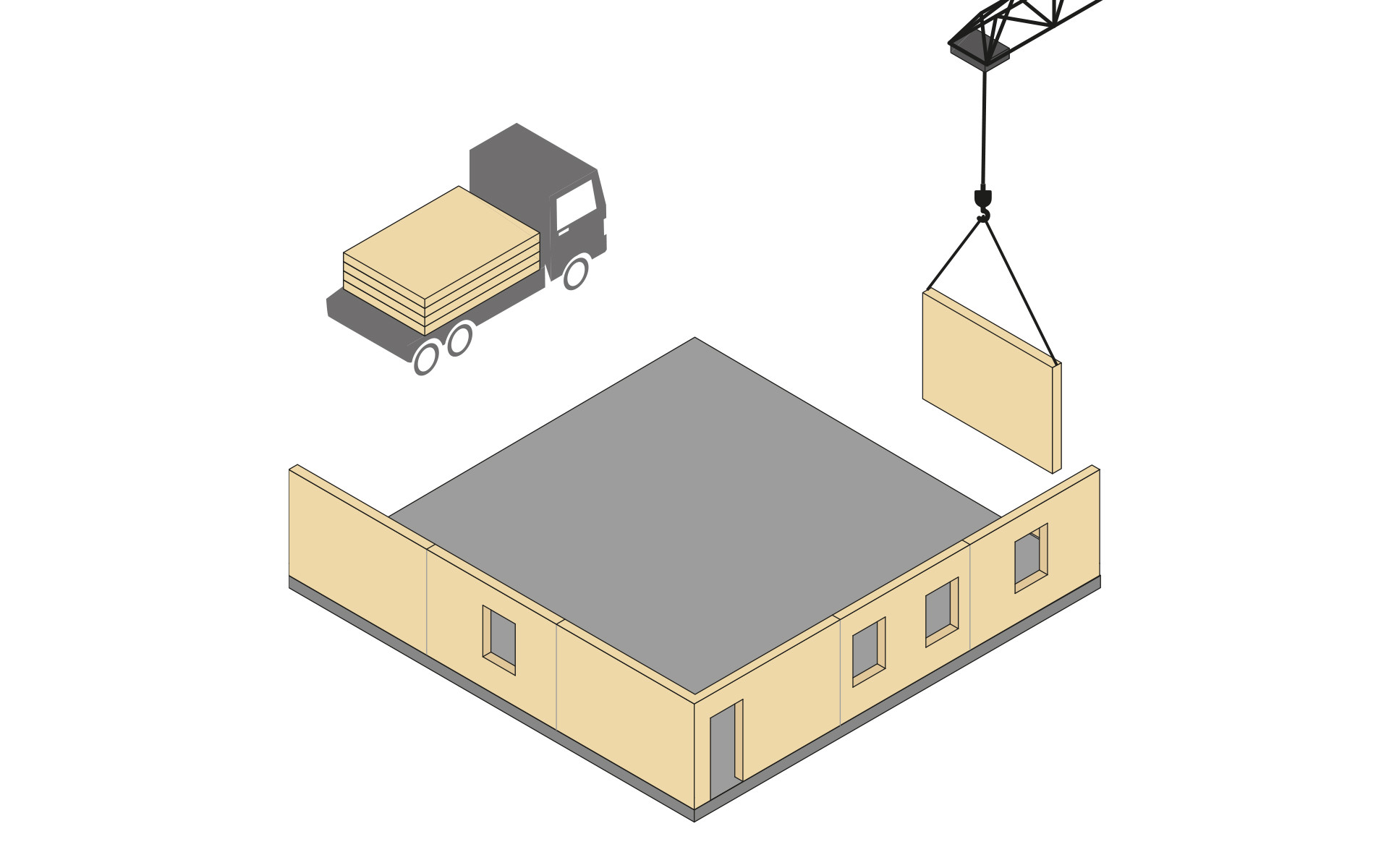
Prefabricated constructions with volumetric (or three-dimensional) modules
The most advanced type of prefabrication involves manufacturing volumetric components at the plant. Once laid and assembled on site, these components form rooms and other building volumes. They can be produced with a very high degree of prefabrication, including interior and exterior finishes, fixtures and fittings. Logistics and transport are crucial for these types of buildings. For this reason, the module connection system can also be used as a lifting and handling system, as is possible with X-RAD.
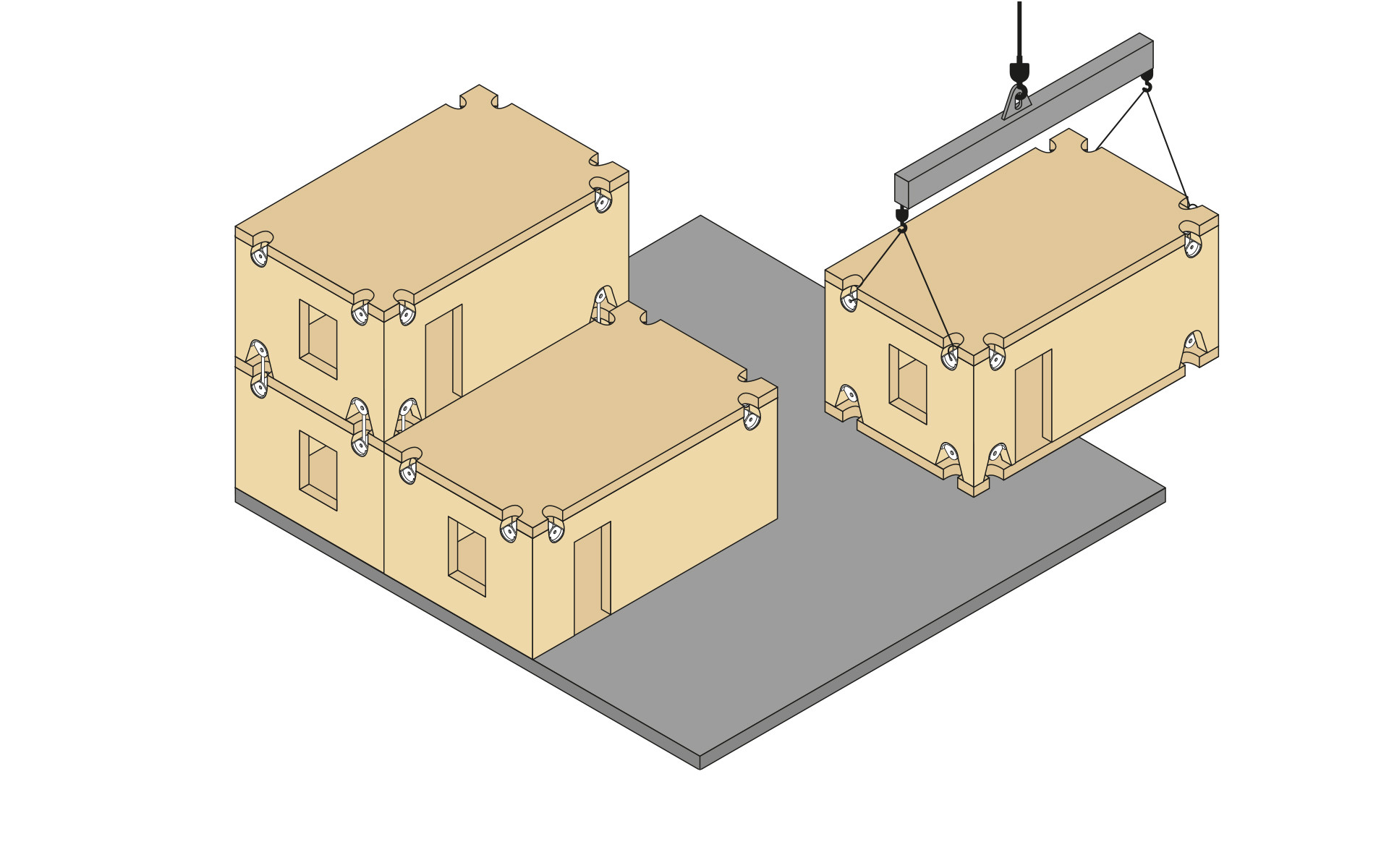
Issues with Design for Manufacture and Assembly (DfMA)
When it comes to timber constructions, one of the main challenges in Design for Manufacture and Assembly (DfMA) is the interaction with concrete, be it the core or the ground connection, and managing the varying tolerances between these materials.
Production tolerances for timber panels and those for concrete walls can vary significantly, potentially causing problems during installation.
If the concrete walls are not perfectly aligned and the timber panels not produced with suitable tolerances, this can lead to problems during assembly and issues with structural stability.
To address these issues, effective communication beforehand among all parties involved is crucial, including installers and those overseeing the concrete works, to establish acceptable installation tolerances.
Moreover, a tolerance recovery plan should be considered to ensure the safety and efficiency of the connections between the timber elements and the concrete structure, regardless of variations in production tolerances.
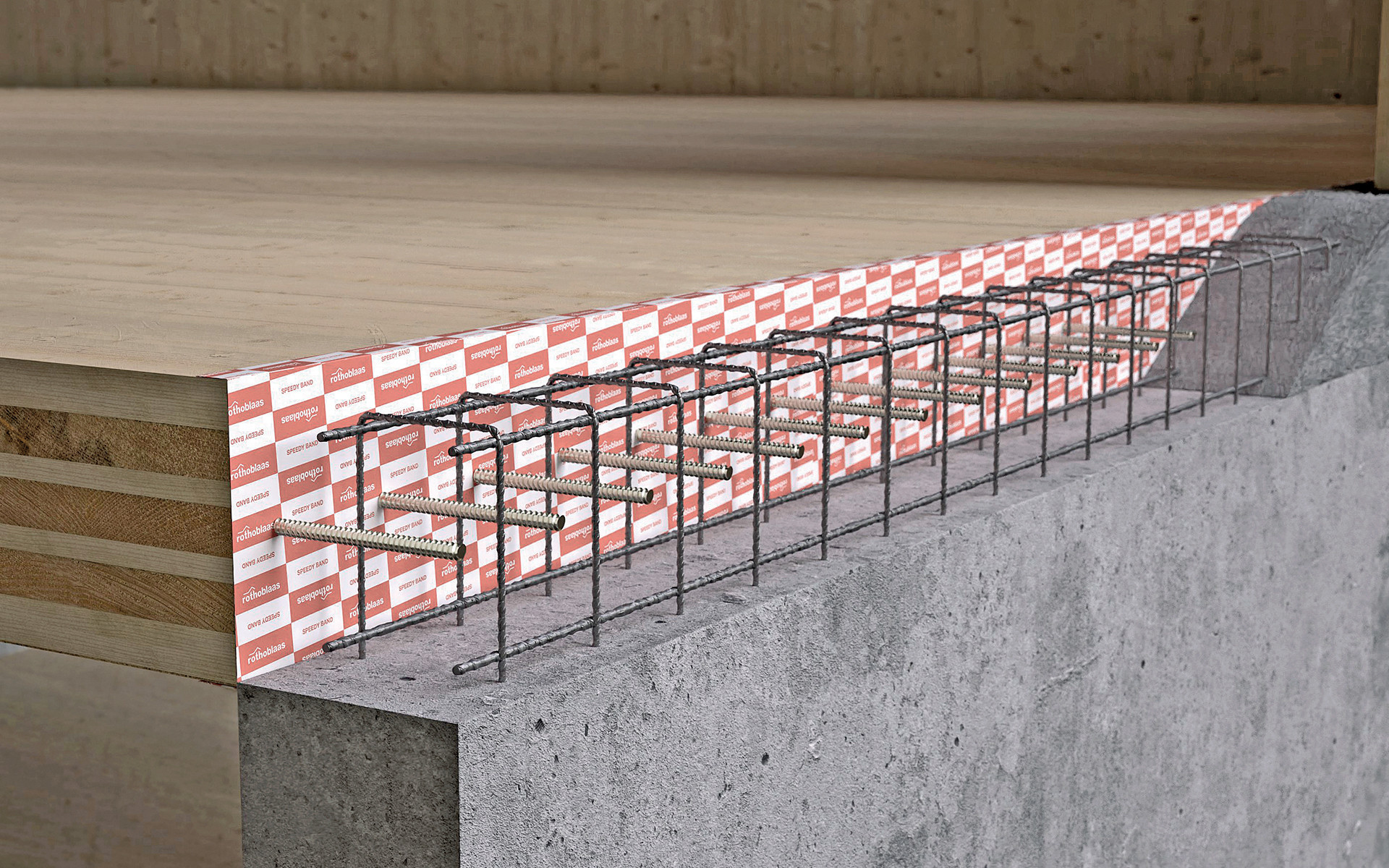
Rothoblaas considers this aspect too in its approach to DfMA, making the construction process more efficient and reducing costs, timing and the risk of error.
All Rothoblaas Design for Manufacture and Assembly solutions can be viewed in our new plates catalogue: LINK
All rights reserved
Technical Details
- Companies:
- Holzbau Layh, BANKWITZ beraten planen bauen GmbH, Furche Geiger Zimmermann Tragwerksplaner GmbH, HolzBauWerk Schwarzwald GmbH
- Country:
- Any
- Products:
- SHARP METAL RADIAL X-RAD